PRODUCTION TECHNOLOGY
Metal coils which enter the panel production line are shaped on the roll formers. And they form the external and internal surfaces of the sandwich panel. After the sheets take its form, Polyurethane (PU)/Polyisocyanurate (PIR) are injected between two surfaces with special systems insulation layer is created with special feeding units. The insulation layer completes its chemical reaction in the press band by entering into the oven and completely adheres to the surface sheets and forms the composite system sandwich panel. The panels are automatically cut in the desired lengths with an automated rotary saw, in a simultaneously continuous line. They are packed and become ready for shipment. Water and sound insulation, fire-resistant types are available. The insulating layers used in manufacturing sandwich panels provide thermal insulation at different levels. It is long-lasting. And environment-friendly. It does not produce and harbor bacteria. Sandwich panel economizes structural and foundation costs since they are light weighted. It is the most ideal building material that can be applied in all structures such as steel, wooden or concrete construction.
Sandwich panels are lightweight but durable construction materials which are formed by taking the best characteristics of their components.The increase in demand for Cold Storage and energy crises occurred at the end of the 2nd World War led to taking the first step of the Sandwich Panel production. Sandwich panel has become a material demanded in constructions upon the fast and modern construction demand; the energy costs arising from the energy crisis worldwide following the 2nd World War and architects’ realization of the sandwich panel’s design elasticity and diversity.
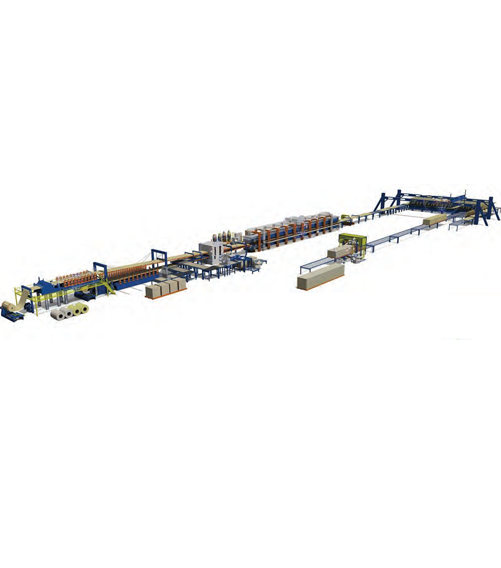